Waterproof Control Cable Ensuring Reliable Performance in Challenging Environments
Introduction (150 words):
In today's rapidly advancing technological landscape, control cables have become an indispensable part of various industries, from manufacturing and automation to telecommunications and transportation. These cables serve as the backbone for transmitting signals and controlling systems, ensuring smooth operations and efficient functionality. However, in many applications, control cables are exposed to harsh environments, ranging from extreme temperatures and humidity to chemicals and water ingress. This often poses a significant challenge to their reliable performance and longevity.
To mitigate these challenges, waterproof control cables have emerged as a game-changer. Designed with specialized Shielded cable with high flexibility and construction techniques, these cables provide protection against water, moisture, and other environmental factors that could potentially impact their performance. This article aims to explore the features, benefits, and applications of waterproof control cables, highlighting their importance in enabling efficient and uninterrupted operations in challenging environments.
Section 1: Understanding Waterproof Control Cables (500 words)
1.1 What are Waterproof Control Cables?
Waterproof control cables are specifically engineered cables that possess enhanced resistance to water and moisture. They are designed to prevent water ingress, thereby safeguarding the internal components and ensuring consistent performance, even in wet or damp conditions. These cables are typically constructed using specialized materials, such as thermoplastic elastomers (TPE) or polyvinyl chloride (PVC), which provide excellent water repellency.
1.2 Features of Waterproof Control Cables
Waterproof control cables exhibit several key features that make them suitable for challenging environments, including:
- Water and moisture resistance: These cables are designed to prevent water ingress, ensuring uninterrupted signal transmission and system control.
- Chemical resistance: Waterproof cables are often resistant to various chemicals, making them suitable for applications that involve exposure to corrosive substances.
- Abrasion resistance: The outer sheath of these cables is manufactured to withstand abrasion, protecting the internal conductors from damage.
- Temperature resistance: They can operate reliably at extreme temperatures, both high and low, without compromising their performance.
- Flexibility and durability: Despite their protective features, waterproof control cables maintain flexibility and durability, allowing for easy installation and long-term use.
Section 2: Advantages of Waterproof Control Cables (700 words)
2.1 Enhanced Reliability
One of the primary benefits of waterproof control cables is their enhanced reliability in challenging environments. They provide a reliable transmission medium for crucial signals, ensuring that control systems function optimally regardless of external conditions. By preventing water ingress, these cables minimize the risk of short circuits, signal loss, and other electrical issues that can lead to system failure.
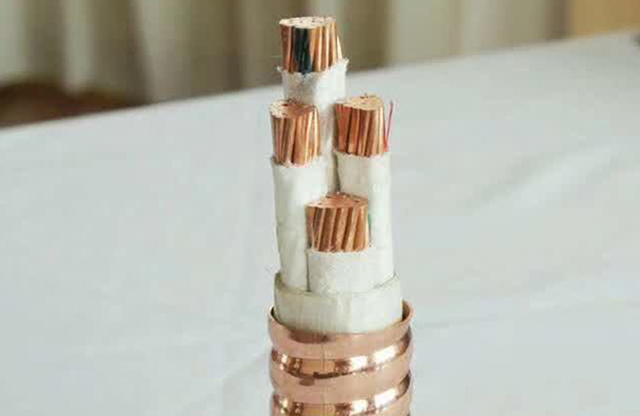
2.2 Extended Lifespan
Waterproof control cables are built to last. Their water and moisture-resistant properties protect the internal conductors from corrosion, which can significantly reduce the lifespan of regular cables. With a longer lifespan, these cables offer cost savings by reducing the need for frequent replacements and downtime.
2.3 Increased Safety
In many industrial applications, safety is paramount. Waterproof control cables play a crucial role in ensuring safe operations by minimizing the risk of electrical faults that could lead to accidents or damage to equipment. By providing reliable signal transmission, these cables contribute to a safer working environment.
2.4 Versatility in Applications
Waterproof control cables find applications in various industries and sectors, including:
- Industrial automation: These cables are widely used in manufacturing facilities, where control systems need to operate reliably in demanding conditions, such as exposure to dust, moisture, and chemicals.
- Transportation: Waterproof control cables are essential in automotive, rail, and marine applications, where they are exposed to constant vibrations, temperature variations, and contact with water.
- Telecommunications: In outdoor or underground installations, where exposure to moisture is prevalent, waterproof control cables ensure uninterrupted communication and network connectivity.
- Oil and gas: In offshore and onshore drilling operations, where exposure to water, oil, and other harsh substances is common, these cables provide reliable control and signal transmission.
- Renewable energy: Waterproof control cables are used in solar power plants, wind turbines, and hydroelectric facilities, where they withstand environmental conditions, such as rain, UV exposure, and temperature fluctuations.
Section 3: Types of Waterproof Control Cables (800 words)
3.1 PVC Waterproof Control Cables
PVC waterproof control cables are cost-effective options that provide good resistance to water and moisture. These cables are typically used in applications that don't require extreme temperature or chemical resistance. They offer flexibility, durability, and ease of installation.
3.2 TPE Waterproof Control Cables
Thermoplastic elastomer (TPE) waterproof control cables are known for their excellent resistance to water, oil, and chemicals. They can withstand a wide range of temperatures, making them suitable for both indoor and outdoor applications. TPE cables offer high flexibility and durability, allowing for easy routing and installation.
3.3 Polyurethane (PUR) Waterproof Control Cables
Polyurethane (PUR) waterproof control cables are designed for applications that require exceptional resistance to abrasion, chemicals, and oils. They offer high mechanical strength and can withstand extreme temperatures. PUR cables are commonly used in industries such as robotics, automation, and heavy machinery.
3.4 Silicone Waterproof Control Cables
Silicone waterproof control cables are specifically designed to withstand high temperatures and harsh environmental conditions. They offer excellent resistance to UV radiation, chemicals, and extreme temperature variations. https://www.jiangyuancables.com/welder-cable/ are commonly used in applications such as lighting systems, industrial ovens, and automotive manufacturing.
Section 4: Factors to Consider in Selecting Waterproof Control Cables (500 words)
4.1 Environmental Conditions
Understanding the specific environmental conditions where the control cables will be installed is crucial. Factors such as temperature, moisture levels, exposure to chemicals, and physical stress should be considered to determine the appropriate type of waterproof control cable.
4.2 Cable Construction
The construction of the cable plays a significant role in its durability and performance. Look for cables with multiple layers of protection, such as a moisture-resistant outer sheath, shielding, and robust internal conductors. The cable's design should ensure a tight seal against water ingress.
4.3 Industry Standards and Certifications
Ensure that the chosen waterproof control cable complies with relevant industry standards and certifications, such as UL, CSA, or IEC, to guarantee its quality and reliability.
4.4 Cable Flexibility
Consider the cable's flexibility, as it can impact the ease of installation and routing. Flexible cables are often preferred, especially in applications that require frequent movement or cable routing in tight spaces.
4.5 Cost Considerations
While the performance and reliability of waterproof control cables are crucial, it is also essential to consider the overall cost, including installation, maintenance, and long-term performance. Choosing a cable that offers the best balance between performance and cost is crucial.
Conclusion (250 words):
Waterproof control cables have revolutionized the way industries operate in challenging environments. These cables provide a reliable and durable solution for transmitting signals and controlling systems, ensuring uninterrupted operations even in the presence of water, moisture, or other harsh conditions. With their enhanced reliability, extended lifespan, and increased safety, these cables have become a vital component in numerous industries, from manufacturing and automation to telecommunications and transportation.
By understanding the various types of waterproof control cables available and considering factors such as environmental conditions, cable construction, industry standards, flexibility, and cost, industries can make informed decisions when selecting control cables for their specific applications. Investing in high-quality waterproof control cables not only ensures reliable performance but also leads to cost savings and improved productivity in the long run.
As industries continue to advance and face increasingly demanding operating conditions, the importance of waterproof control cables cannot be overstated. These cables play a pivotal role in enabling seamless operations, safeguarding critical systems, and maintaining productivity in environments where water and moisture pose significant challenges.